Since the beginning of civilization, materials found near the Earth’s surface were used to make tools for wealth and trade. Materials like clay, stones, and metals were used to make weapons vessels, and goods.
The mining industry discovers and extracts naturally occurring minerals from the Earth. The extraction of such minerals is the fundamental function of this industry. Industrial robotics growing very fast in this decade. New Innovative machinery is used to make complex tasks easier which was hardly done by humans in the past.
Traditional mining methods contribute to increased shipping costs, decarbonization programs, and input costs. Companies need to focus on more productivity and reduced operational costs to boost profitability. This can be optimized by using digital technologies. With Robotics In Mining, mining companies will be able to fill the gaps in their productivity and increase profitability.
Current State of Mining Industry
Digital systems not only increase profits but also make mines safer, cleaner, and more efficient. Innovations on the Internet of Things have transformed mining. In the past workers used to dig by hand and now use automatic vehicles to investigate deep tunnels. Moreover, robotics are now being used to control multiple rigs at once.
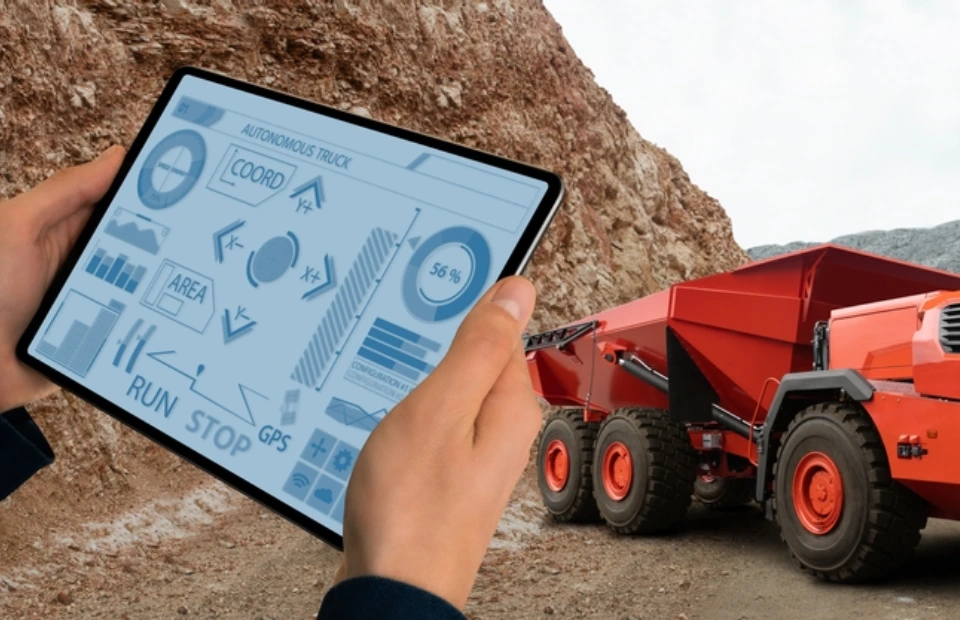
The innovations in the mining industry are replacing workers in the field with robots, still, they are providing the industry numerous benefits. In this way, robotics is saving human lives whilst increasing productivity. As a result, businesses can grow by generating more profits by using robots during the operational hours of the industry.
Role of Robotics in Mining
Robotics play an important role in mining. In the past, it was very hard for humans to perform mining operations but with the help of robots, it has become simple and easy.
Robotics Integration in Mining
Robotics has offered solutions to cope with the inherent dangers and significant expenses that come with mining. They are transforming mining into an efficient and cost-effective industry. Integration of robotics in mining provides the following set of benefits:
- Environmental Benefits
Robotic systems minimize material wastage by:
Minimizing fuel consumption, optimizing routes, and reducing energy emissions.
Example: The Hammerbot uses energy in compressed gas to break the rocks.
- Improved Safety Measures
The risks associated with mining are mitigated by using:
Autonomous vehicles. These machines operate effectively in underground mines, reducing human exposure to danger.
- Greater Accuracy and Productivity
Robotic equipment performs human operations in terms of precision increases the overall quality of operations and enhances productivity.
Example: A digital drilling machine can provide accurate figures of diameter holes in rocks ensuring accuracy. It also provides consistency to lose or fragment the material ensuring uniform results.
- Improved Efficiency
Robotic systems and autonomous vehicles can work 24/7 frequently without any breaks. It prevents shift changes and maximizes productivity. Unlikely humans, automatic systems can perform smoothly and efficiently.
- Reduced Cost
The replacement of human workers with robotics and autonomous vehicles decreases human effort which in turn decreases the labor cost. It reduces the dependency on human operators by reducing the number of staff working in the mining industry. Moreover, optimized routes and reduced movements lower fuel consumption and maintenance expenditures.
Case Studies of Successful Robotic Implementations
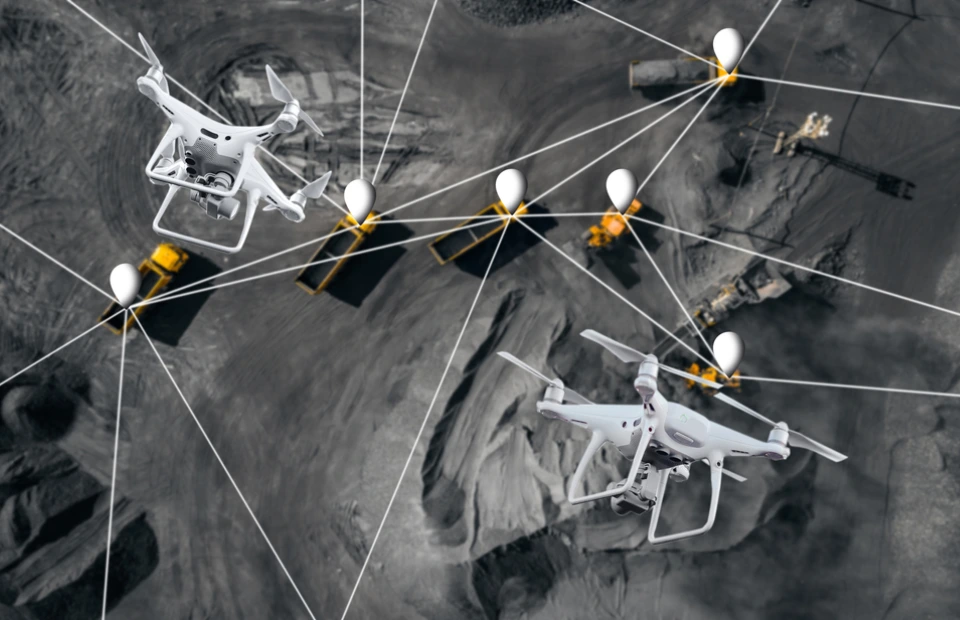
Autonomous Mining Vehicles
Autonomous vehicles operate without human drivers, reducing the risk of accidents. They support extreme environmental conditions such as extreme temperatures, and lots of dust, aiding efficient operations, and navigation.
Rio Tinto is a successful mining company that has employed autonomous trucks since 2008. These vehicles operate round-the-clock, significantly improving productivity. Rio Tinto’s autonomous drilling systems provide greater accuracy and improved efficiency in remote drilling systems.
Robotic Mining Equipment
Robotic Mining Equipment can be remotely controlled or operated independently performing different tasks such as drilling, blasting, excavating, etc.
Sandvik, a Swedish mining company has developed remote-controlled drills, rigs, and loaders. These machines excel in hazardous environments exceeding human workers in speed and efficiency.
Inspection and Maintenance Robots
These robots play a fundamental role in ensuring the safety and reliability of mining operations. They conduct overall inspections of infrastructure without human interference to ensure safety.
ABB, a Swedish multinational company, has developed robots to traverse pipes and tunnels. They inspect for damage to improve safety standards rather than relying on human operators.
Emerging Technologies in Robotics
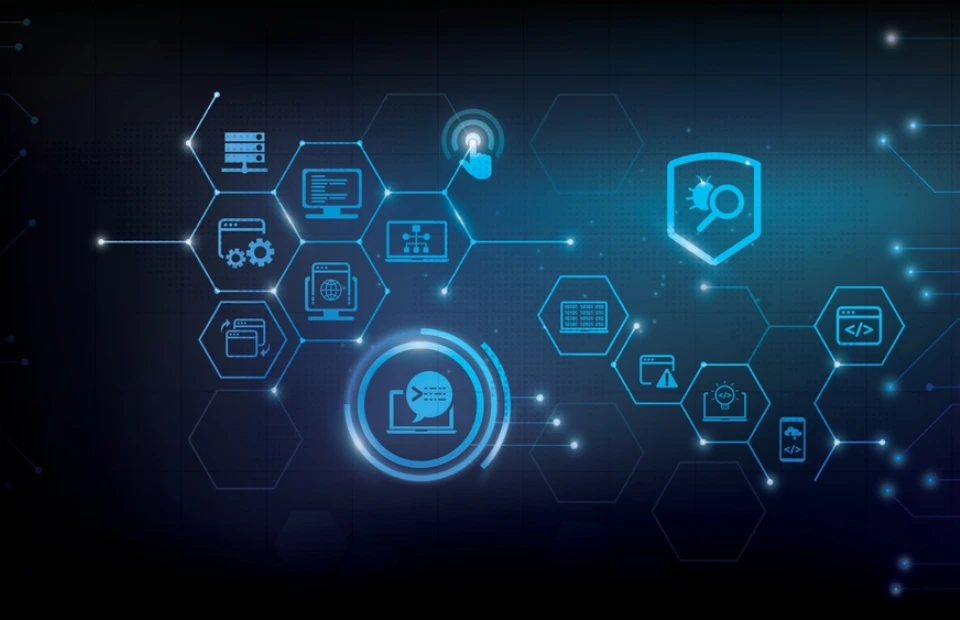
Remote mining vehicles and autonomous haul trucks are key innovation areas in robotics. Mining is becoming safer and more productive as a result of the Internet of Things and plasma.
AI-driven autonomous machinery
Robotic devices powered by artificial intelligence can operate a wide range of tasks such as:
- Drilling
- Blasting
- Hauling
- Bolting mine roofs
- Ore sampling
- Rescuing trapped miners
Autonomous Load Haul Dump (LHD) vehicles using robotics have been developed by several research multinational companies, such as Atlas Copco and Sandvik Mining.
Use of the Internet of Things
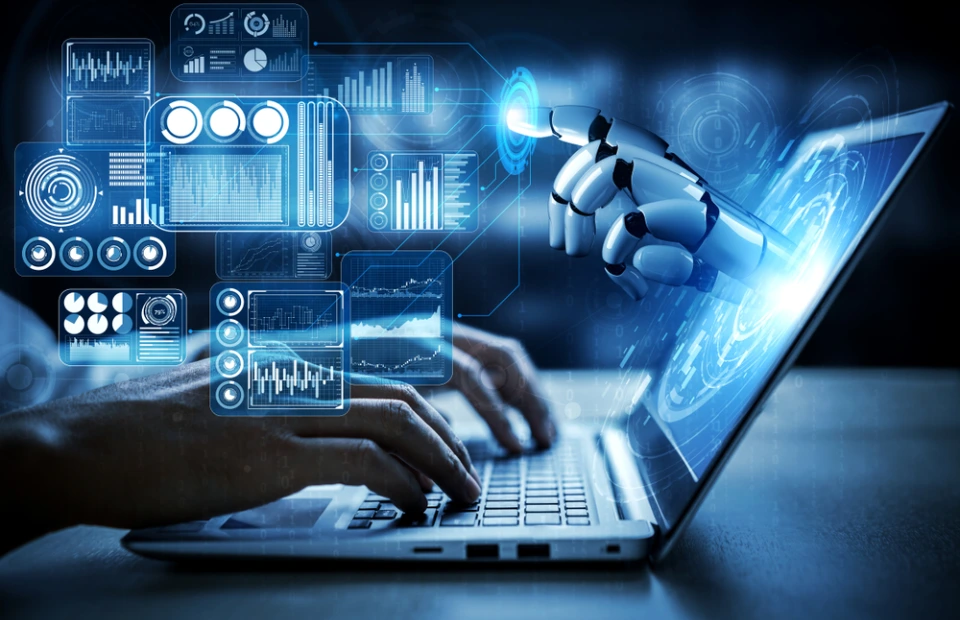
This technology is based on the convergence of wireless technologies such as the Internet to connect machines. Sensor technologies automatically transfer and receive data over a network without needing to perform human-to-human or human-to-computer interaction. These technologies enable computers to observe, identify, and understand different aspects of mining. This improves the traceability and visibility of the entire mining operation.
Networking companies like Cisco are working in close coordination with other industries to deliver IoT-based solutions specifically for the mining industry.
Advanced airborne gravity gradiometer technology
The University of Western Australia in collaboration with Rio Tin developed this advanced gradiometer technology to find solutions to mineral exploration changes. It is known as a VK1 airborne gravity gradiometer. It measures subtle changes in the Earth’s gravity field to identify ore bodies that are hard to detect. These devices are expected to have further success in exploration efforts by mining companies.
3D Imaging Technologies
3D printing and imaging technologies have contributed to the exploration of large mines. Applications of 3D imaging technologies are used for studying the geology of potential mining areas. Seismic surveys have improved the efficiency of these studies greatly. New emerging technologies such as 3D laser scanning help to capture spatial data using laser light. It also enables geologists to build 3D geological maps merging the surface mapping data.
Plasma Technologies
The plasma process increases the production of precious metals from complex ores, such as gold, silver, and platinum. US company, Toss Plasma Technologies (TPT) has developed a new plasma technology by which complex ores such as zinc, nickel, copper, and lead are heated applying ultra-high temperatures.
Challenges and Considerations
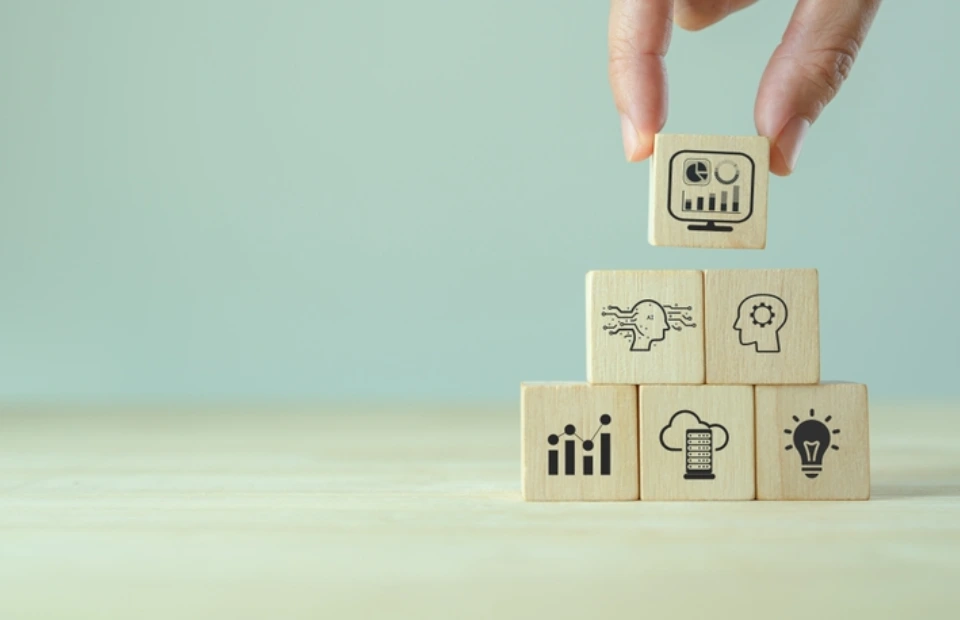
Addressing concerns and challenges
While robotics provides numerous benefits for the mining industry, it still encounters several challenges and limitations. These include the high investment costs needed to buy these autonomous machines and digital technologies. There is also a need to have expertise in using these devices for which companies must provide a high budget.
Mining companies need to collaborate with experts to consider financial allegations to leverage the potential of robotics fully.
Regulatory Considerations
We must face the challenges associated with investment costs and specialized expertise requirements. But engineers can play a vital role in reducing the impacts of these challenges. They can use their expertise to develop efficient and optimized systems. This ensures the safety of the mining industry and addresses that it can fully exploit the benefits of robotics.
Moreover, with ongoing innovations robotics continue to transform mining enhancing the potential for increased productivity, improved safety, and sustainable practices.
Industry Adoption and Investment
Automated mining systems are adopted in developed countries like Australia and the United States. Also, stakeholders are dedicated to adapting autonomous mining systems in African countries. In a developing country like Pakistan, there is a focus on exploring the understanding of autonomous mining systems and the level of preparedness of stakeholders to adopt this latest technology.
Almost a decade last year, demand for lithium, copper, and other minerals resulted in a great deal of investment. These minerals are required for energy transition. The world’s top 40 mining companies invested about $85 billion worldwide in 2022 according to the report published in June by consultancy PwC. This has been the greatest investment since 2014.
Conclusion
Robotics are designed and manufactured to perform repetitive tasks, but the human brain is not. Mining companies are now using robots and autonomous machinery to complete tedious tasks and redundant operations.
Robots and machines with efficient capabilities may have a wider range of applications in the future. Those robots would be better suited for more difficult and dynamic activities. They could be able to learn new practices, quickly adapt to the environment, and change their behavior. Robotics will enhance the standard of living!
Frequently Asked Questions on Robotics in Mining
How can robotics help address challenges in mining operations?
Robotics can help address challenges in mining operations by optimizing resource extraction processes, mitigating geological and operational risks, increasing operational transparency and accountability, and enabling remote monitoring and control of mining activities in challenging or hazardous environments.
What role does data analytics play in robotics for mining?
Data analytics plays a crucial role in robotics for mining by analyzing large volumes of sensor data collected from robotic systems, mining equipment, and environmental sensors to optimize operational performance, predict equipment failures, identify opportunities for process improvements, and support decision-making in real-time.
Are there any potential drawbacks or challenges associated with robotics in mining?
Potential drawbacks or challenges associated with robotics in mining include the high initial investment costs, the need for specialized expertise in robotics and automation, regulatory and safety considerations, potential job displacement or changes in workforce dynamics, and concerns about cybersecurity and data privacy in autonomous mining systems.